automatic eps foam plastic thermocol making machine for styrofoam packaging
Product Description
Main Features of eps foam plastic thermocol making machine
Unique machine structure:
a. High-strength frame: The further enhanced back frame and moving frame, the whole eps thermocol making machine adopts the body and foot, and makes the frame and machine feet integrated, This greatly increases the frames strength and sturdiness of the eps thermocol making machine.
b. The eps thermocol making machine are treated with zinc spraying after the manufacturing works which improves load life of the eps plastic thermocol making machine.
c. The styrofoam moulding machine with vacuum adopts opposite directions type tie bar for easy maintenance and wear resistance. The self-lubricating copper tube solves original tie bar bushing’s problem and improves the lubrication effectiveness of the eps plastic thermocol making machine.
d. The preventing plate and back mould plate of the eps plastic thermocol making machine with vacuum are all stainless steel, which reduces the wear and rust of the mold precision.
Hydraulic Pressure System:(save 6S/cycle):
a. Compared to the T and A type machine, our new E type styrofoam packaging machine with hydraulic system achieves faster operation for 250mm/speed from 180mm/second. The eps styrofoam packaging machine with vacuum can effectively improve production efficiency.
b. Hydraulic cylinders for the machine frame movement have safety locking of the mold during the steaming process and avoids the leakage of steam of the eps styrofoam packaging machine.
c. Special hydraulic pressure design: the ejecting cylinder and de-mold cylinder can be running simultaneously, which senses the de-mold gas blowing and product ejection synchronization effectively, reducing running time and improves de-mold capability of the eps styrofoam packaging machine.
Steam System:(ensure stable and less steam consumption)
a. Fang-Yuan patented PID system made by DN50 actuator makes the sensitive steam pressure control between 0.10-0.15Mpa,+/0.1Mpa tolerance giving us reduced heating time saving around 25%-30% of energy consumption.
b. The thermocol shape moulding machine controls the steam pressure by balance valve and pressure sensor instead of electronic connector pressure gauge. The mold pressure of the EPS moulding machine can be set by touch screen to make easy and accurate control.
Piping System:
a.For the complete inlet and outlet of water, air and steam, we use big pipeline and vales which are very close to the mold, reducing the excess energy consumption, while improving running speed of the eps plastic thermocol making machine.
Vacuum System:
a.The eps plastic thermocol making machine adopts vertical vacuum system, with 4-6” large drain pipeline and long length of condensation drainpipe. The vacuum tank is equipped with a big spraying system, which sprays the rising hot steam directly, and increases condensation rate. Thus, improving vacuum suction efficiency and achieves vacuum as main cooling instead of main water cooling(normally water cooling will be set only 8-12s). This enables the product of water percentage≤10%,In addition, the spray header of the eps plastic thermocol making machine’s replacement and maintenance is very convenient.
Control System:
a. All pressure adjustments of EPS eps plastic thermocol making machine are remote controlled by the control box, such as cross steaming, Main steaming, Filling also adjusted in touch screen according to different foaming area. The program of the eps plastic thermocol making machine also has many self-protection and alarm systems.
b. The eps plastic thermocol making machine adoptes remote control system for all control pressure parts, electrics parts, valves, gauges and hydraulic parts sourced from famous international brands with quality to ensure the eps plastic thermocol making machine stable and smooth running.
We do have a qualified group of English, Russian, Indian, Arabic speaking engineers and an able salesstaff that support us around the world. We set sales and service office in lndia, Iran, Syria, Egypt etc.
Founded in 1988,over 600 staff and covered 100,000 sqm Workshop.
Professional EPS, EPP, EPO, ETPU machinery manufacturer integrating R & D, production, sales andservice delivery, provides our clients with system solutions including design, training, operation and turn-key projects.
Yearly around 2,200 sets machines outputs.
Exported to more than 103 countries.
The first drafter of National lndustry Standard of EPS machinery in China.
Since 1988, More Than 50,000 Units Equipment in 103 Countries and Area.
FANGYUAN boasts a pool of fine teams, with qualified EPS/EPP products as to moulds, equipment,resources, technologies, and with rich experience at production and operation.
PRE-SALES SERVICE
Inquiry And Consulting Support
Lastest Industry Trends
Offer Turn-key EPS Plant
Sample Testing Support
View Our Factory
Suggest Layout Support
AFTER-SALES SERVICE
One Year Warranty
Machine Test Video Before Delivery
English Manual, Electric Diagram Training How To Install And Running The Machine
Engineers Available To Service Machinery Overseas
24 Hours Online Service
130,000 ㎡ Workshop.
Yearly Around 2,200 Sets Machines Outputs.
24 Hours Technical Supports and Aftersales Service.
Professional Maintenance and Offer All Kinds of Spare Parts
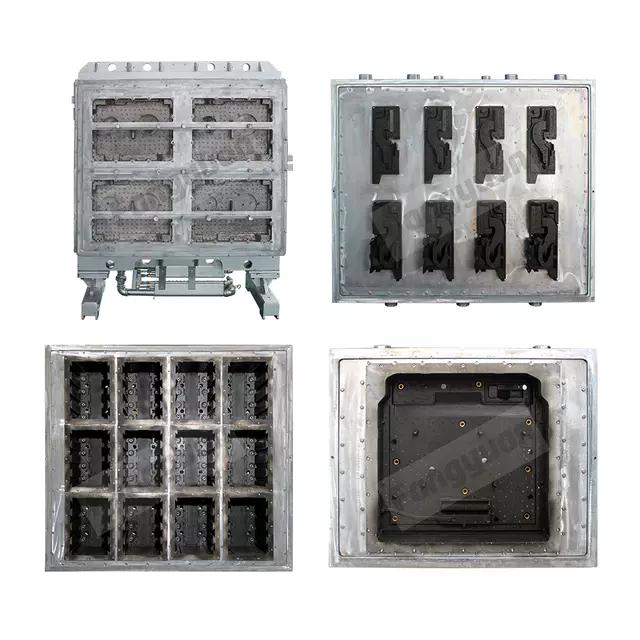